Improved results of Large Diameter Welding neck Flange
In view of the flange deformation problem in Large Diameter Welding neck Flange welding, our company's production department has conducted in-depth research. This problem has been thoroughly solved and the qualified rate of products has been raised to over 99.99%. As a company with 36 years of production experience, continuous process improvement and scientific research make our responsibility and mission. In the French industry, we must always be a contributor and leader.
Reasons of deformation
When Large Diameter Welding neckFlange and stainless steel cylinder are welded, it takes too long to complete a circle of welding due to the large diameter of flange, poor rigidity and long weld bead. In the welding process, the heating and cooling speed of fusion zone and the cooling time interval of discontinuous welds are too long, which results in the unbalanced heating of the whole girth. The shrinkage and deformation of weld seam are not uniform.
The circumferential welding shrinkage of flange welding zone is very large when the circumferential heating part of flange welding zone iscooled byweld seam, which further aggravates the expansion of deformation. The flange forms irregular ellipse phenomenon in circumferential direction, local concave and part convex. At the same time, because of the welding shrinkage force, the inner circumference of the flange becomes smaller, while the outer flange is in a lower temperature, so the heat input of the flange is small, the rigidity is good, and there is no shrinkage basically; thus, the flange section is twisted and the flange surface is reversed remarkably, at the same time, the central axis of the bolt hole of the flange is no longer with the axis of the cylinder body. Parallel. Facts have proved that the overturning force is very large. After welding the groove of the upper flange section with the cylinder body, it is still impossible to make any improvement on the deformation.
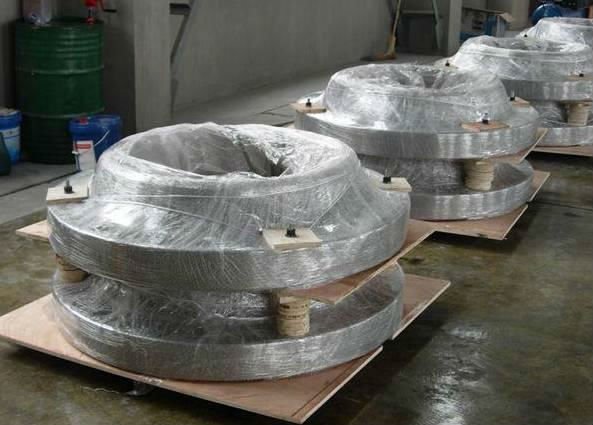
Large diameter flat welded flange and similar large diameter annular workpiece, due to the poor rigidity of the structure itself, are prone to deformation when the rigidity is not strengthened and local heat input is uneven. The amount of deformation varies according to the heat input. For this kind of workpiece, the relative diameter is much smaller. Make it rigid enough before welding or heating. At the same time, the input quantity of heat, the uniformity of heat input and the slow cooling after heating should be controlled during welding and heating.
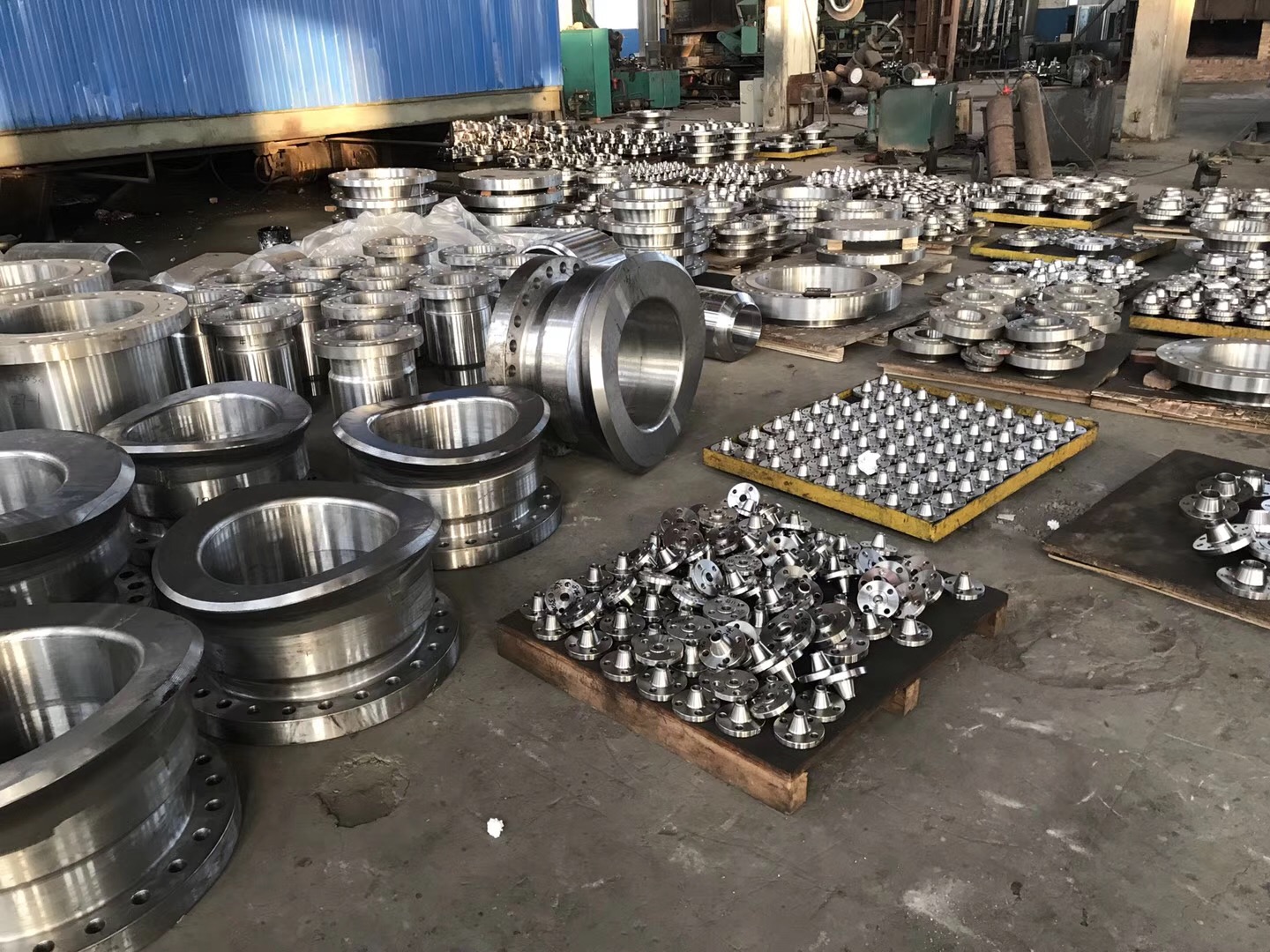
Improvement of Welding Technology for Large Diameter Butt Welding Flange
The assembly and welding procedure of flange and pressure vessel cylinder are as follows: (1) machined flange is finished product; (2) riveter alignment group to flange and cylinder joint; (3) manual welding of flange and cylinder joint weld; (4) dimension inspection after welding, leak detection air tightness inspection; (5) welded flange stainless steel lining ring; (6) machined lining ring. Sealing surface.