Welded steel pipe arrival and test
After seamless pipe raw materials purchase, today seamless pipe raw materials to the factory again. For some water conservancy projects and other low-pressure pipeline projects, domestic and foreign technology in recent years will generally procure enough technical parameters, relatively low-cost straight seam steel tubes and fittings. Therefore, in the face of the next China Environmental Protection month, our company also makes stock storage in advance. According to the requirements of the company, the straight pipe stock has been strictly checked.
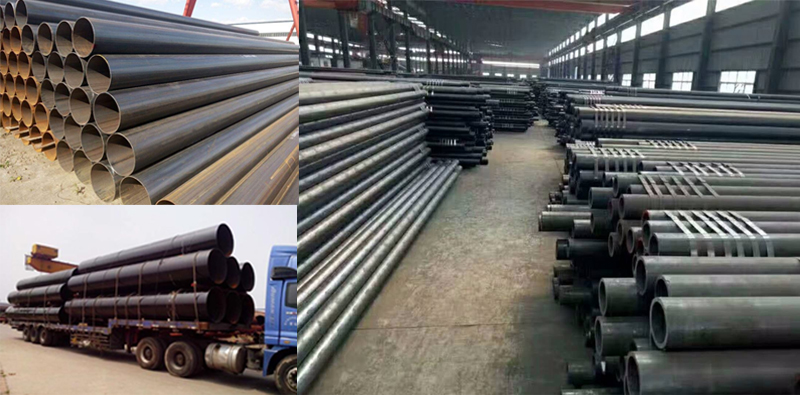
Commonly used detection methods for Welded steel pipe are:
There are many kinds of Welded steel pipe quality inspection methods, among which physical method is also the most commonly used inspection method. Physical inspection is the use of some physical phenomena for testing or testing methods. Generally, NDT is used. The current NDT includes magnetic flaw detection, ultrasonic flaw detection, radiographic inspection, penetrant flaw detection and so on. The following straight seam steel pipe factory introduces you in detail:
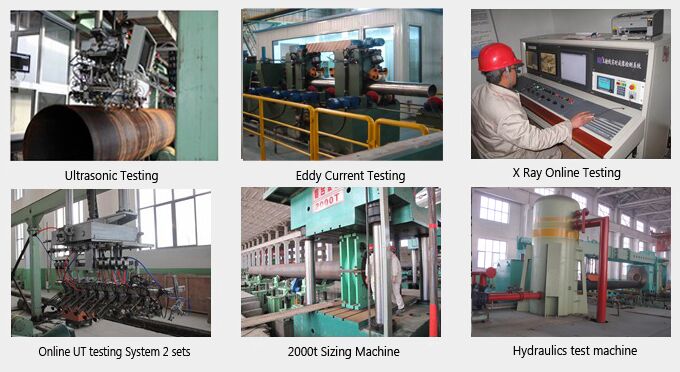
Magnetic force test
Magnetic flaw detection can only find defects on and near the surface of magnetic Welded steel pipe, and can only do quantitative analysis of the defects, the nature and depth of the defects can only be estimated according to experience. Magnetic testing is the use of magnetic field magnetized ferromagnetic straight seam pipe produced by magnetic flux leakage to detect defects. According to the different methods of magnetic flux leakage measurement, it can be divided into magnetic powder method, magnetic induction method and magnetic recording method, among which magnetic powder method is the most widely used.
Ultrasonic examination
In the propagation of ultrasonic wave in Welded steel pipe and other homogeneous media, reflection occurs at the interface of different media, so ultrasonic wave can be used to detect internal defects. Ultrasound can inspect any welding material, any part of the defect, and can be more sensitive to find the location of the defect, but the nature of the defect, shape and size is difficult to determine. Therefore, ultrasonic inspection of straight steel pipes is often used in conjunction with radiographic examination.
Ray flaw detection
X-ray flaw detection is a kind of flaw detection method which uses the characteristics of ray penetrating material and attenuation in material to find defects. According to the different rays used in flaw detection, it can be divided into three kinds: X-ray flaw detection, gamma-ray flaw detection and high-energy ray flaw detection. Because of the different display methods, each kind of X-ray flaw detection is divided into ionization method, fluorescent screen observation method, photography method and industrial television method. X-ray inspection is mainly used to inspect the cracks, incomplete penetration, porosity, slag inclusion and other defects in Welded steel pipe weld.
Osmotic test
Penetration testing is to detect and display Welded steel pipe defects by using the permeability of certain liquids and other physical properties, including coloring test and fluorescence detection, which can be used to check the surface defects of ferromagnetic and non-ferromagnetic materials.
Previous:Facing environmental regulation, raw materials reserve
Next:Carbon steel pipe fitting exported to Indonesia
Next:Carbon steel pipe fitting exported to Indonesia