Customized products
Steel pipe fittings
SPECIFICATIONS
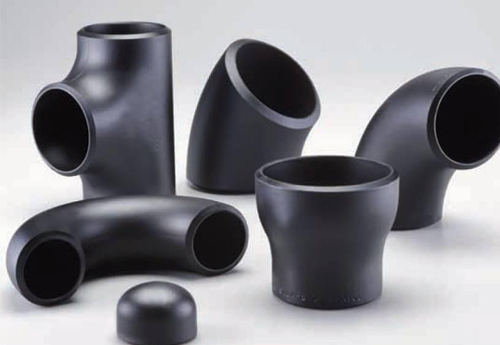
Steel pipe fittings
As a manufacture of steel pipe fittings. We produce all kinds and all size of pipe fittings for more than 36 years. The principle that is generally followed in purchasing is that 1 inch steel pipe fittings always connect to 1 inch pipe line, such as 1 inch elbow, tee, reducer, cap. Many customers are also according to engineering needs, according to the requirements of engineering designers for pipe fittings procurement.
Production process of steel pipe fittings
Blanking
The materials used for pipe fittings are mainly pipes, plates and bars, and the cutting method is selected according to the material characteristics and the shape of the blank used in the products. The shape, size and other requirements of the billet are carried out according to the technological requirements of different products.
For pipes, common cutting methods include band sawing machine or bow sawing machine cutting, gas cutting and plasma cutting.
For sheet metal, the common cutting methods include gas cutting, plasma cutting and punch punching. For bar, the commonly used cutting method is band saw or bow sawing machine cutting, punching and shearing.
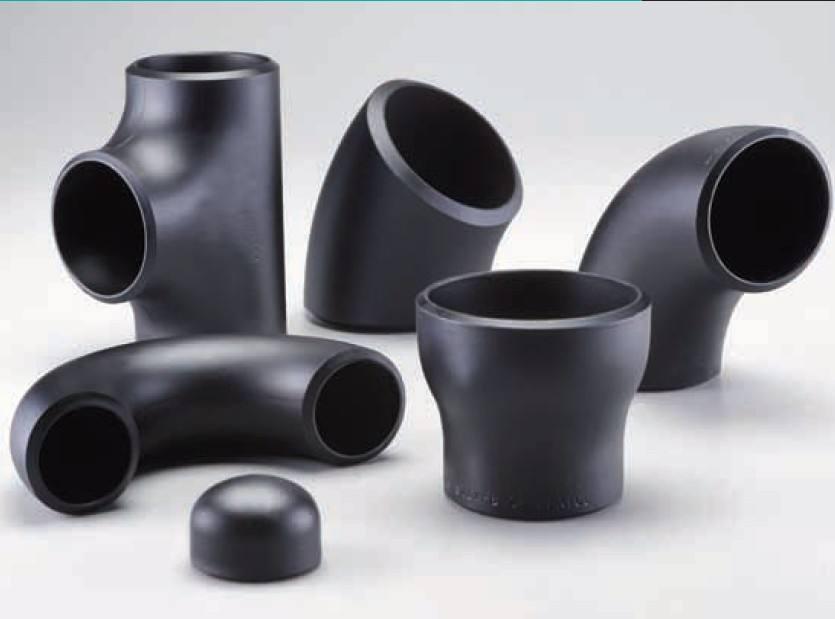
Forming (welding)
For all pipe fittings, forming is an indispensable process. The forming process of different products is not the same.
A. heating
In order to meet the requirement of material deformation in hot forming process, the billet should be heated when forming. Heating temperature is usually determined according to material and process requirements.
When the hot bending elbow or hot bend pipe is formed, medium frequency or high frequency induction heating is usually adopted, and the method of flame heating is adopted. This heating method is continuous heating with the forming process of elbow or elbow, and the tube billet is heated and completed during the movement. 1 inch steel pipe fittings is much easier than other bigger size.
When hot pressing bends, hot pressing three or forgings are formed, the reheating method of the reflector, the method of flame heating, the method of induction heating, or the heating method of the electric furnace are usually used. This kind of heating is to heat the tube billet to the required temperature in advance, and then put it into the mold to press or forge it.
B. Welding
The pipe fittings with weld seam include two cases. One is pipe made with welded pipe. For pipe fittings, the forming process of welded pipe is basically the same as that of seamless tube. The forming process of pipe parts does not include welding procedure; the other is the welding procedure required by pipe fittings to complete tube forming. After a single chip is pressed, the elbow formed by assembling and welding is then welded into steel billets and then pressed by the steel plate, and then the three links are pressed.
Pipe fittings are usually welded by manual arc welding, gas shielded arc welding and automatic welding.
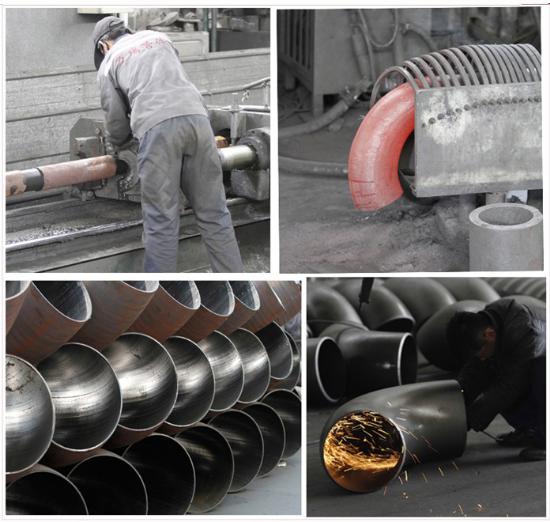
1 inch steel pipe fittings is the most common size.
The manufacturing plant should prepare welding procedures to guide the welding work and evaluate the welding process according to the requirements of the corresponding specifications to verify the correctness of the welding procedures and evaluate the welding ability of the welders. Welders engaged in pipe welding operations shall be able to engage in the welding of relevant steel through the examination of the quality and technical supervision department and the corresponding qualification certificates. (according to the regulations of some industries, the welding pipes in some industries should be used to obtain the welder examination and welding technical evaluation, such as the welding of vessel fittings. " The welder examination and welding procedure qualification of the corresponding classification society must be obtained.
Heat treatment
Heat treatment process is an important part of pipe manufacturing. Through the heat treatment steps of heating, heat preservation and cooling, the processing hardening, residual stress and metal deformation defects produced in the forming process are eliminated, and the metal structure and properties of the tubes after forming are changed, the state before the deformation processing is restored or the performance is improved and raised.
The commonly used heat treatment equipment is a reverberatory furnace, electric furnace, and so on. The usual control mode is that the thermocouple in the furnace is connected to the control device of a temperature time automatic recorder through a sensor. The heat treatment of 1 inch steel pipe fittings is much easier than other bigger size.
There are different regulations for heat treatment in different product standards. Not all deformed tubes are heat-treated. Usually, when the final forming temperature is not less than 723 degrees C (recrystallization temperature) for a tube of low carbon steel, the heat treatment can not be done, because the final state of the tissue is basically a normalizing state under this temperature, below this temperature or higher than 980. Heat treatment should be carried out; the alloy steel or stainless steel fittings should be heat-treated, whether in cold forming or hot forming.
The conventional inspection of heat treatment is usually done by hardness test.
Surface treatment
The surface treatment of pipe fittings is usually made of sand blasting, shot blasting, grinding and pickling to remove the rust and scratches on the surface of the product, so as to make the product smooth and meet the requirements of subsequent processing and inspection.
The surface hardness of tube parts treated with shot blasting is slightly increased.
Cutting machining
Cutting process is the process to finish the welding end, structural dimension and geometric tolerance of pipe fittings. For some pipe products, machining includes internal and external diameter machining. The cutting process is accomplished mainly by special machine tools or general machine tools. For too large size pipes, other methods can be used when the existing machine tools can not meet the processing requirements. For example, the method of grinding after gas cutting is used for large caliber elbow.
The appearance and size inspection of pipe fittings is usually done after cutting.
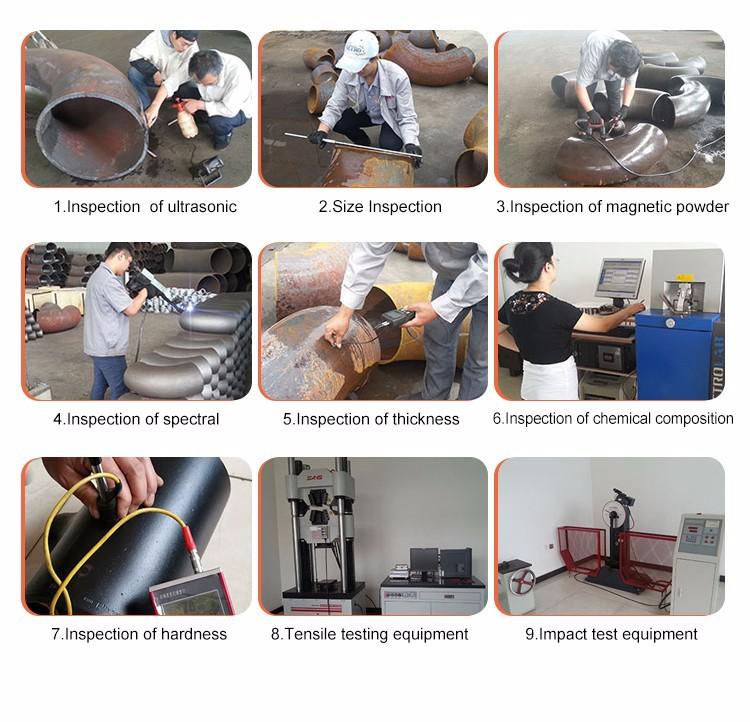
Nondestructive testing
Nondestructive testing is an important procedure for testing defects that may occur in the process of material and pipe fittings. The requirements of NDT for most pipe fittings standards are specified, but the requirements are not consistent. In addition to non-destructive testing of product standards and order requirements, some manufacturers with more stringent quality control also make nondestructive testing requirements according to the material, processing technology and internal quality control regulations to ensure the quality of the factory products. 1 inch steel pipe fittings is the most common products. In actual work, the determination of qualified grade of pipe nondestructive testing should be specified according to the order requirements or standards. Because the surface of the pipe is basically the state of the original tube, plate or forgings, for nondestructive testing of the surface quality of the pipe (MT, PT), the requirement of no definite grade can be classified as grade II. However, no matter how the qualified grade is specified, it is not easy to determine the depth of the interlayer and the crack.
Production process of steel pipe fittings
Blanking
The materials used for pipe fittings are mainly pipes, plates and bars, and the cutting method is selected according to the material characteristics and the shape of the blank used in the products. The shape, size and other requirements of the billet are carried out according to the technological requirements of different products.
For pipes, common cutting methods include band sawing machine or bow sawing machine cutting, gas cutting and plasma cutting.
For sheet metal, the common cutting methods include gas cutting, plasma cutting and punch punching. For bar, the commonly used cutting method is band saw or bow sawing machine cutting, punching and shearing.
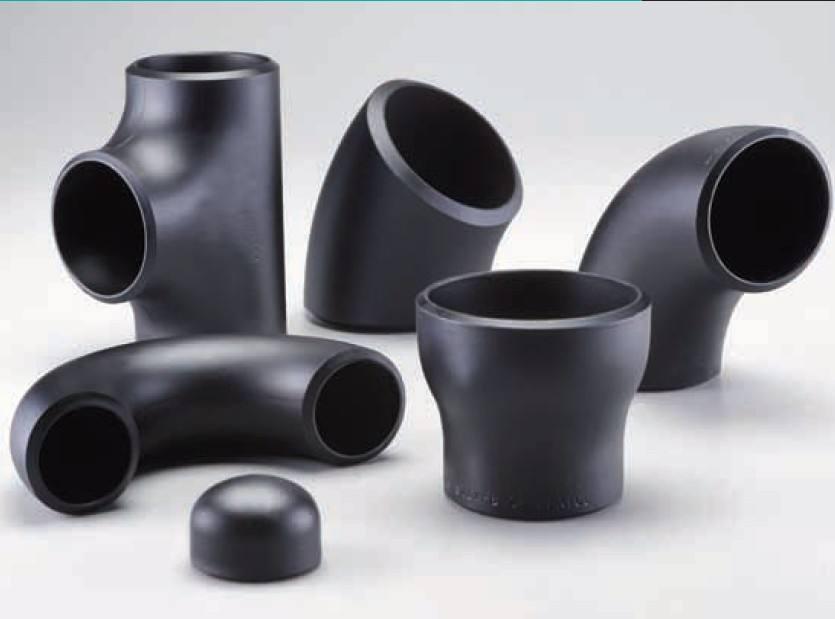
Forming (welding)
For all pipe fittings, forming is an indispensable process. The forming process of different products is not the same.
A. heating
In order to meet the requirement of material deformation in hot forming process, the billet should be heated when forming. Heating temperature is usually determined according to material and process requirements.
When the hot bending elbow or hot bend pipe is formed, medium frequency or high frequency induction heating is usually adopted, and the method of flame heating is adopted. This heating method is continuous heating with the forming process of elbow or elbow, and the tube billet is heated and completed during the movement. 1 inch steel pipe fittings is much easier than other bigger size.
When hot pressing bends, hot pressing three or forgings are formed, the reheating method of the reflector, the method of flame heating, the method of induction heating, or the heating method of the electric furnace are usually used. This kind of heating is to heat the tube billet to the required temperature in advance, and then put it into the mold to press or forge it.
B. Welding
The pipe fittings with weld seam include two cases. One is pipe made with welded pipe. For pipe fittings, the forming process of welded pipe is basically the same as that of seamless tube. The forming process of pipe parts does not include welding procedure; the other is the welding procedure required by pipe fittings to complete tube forming. After a single chip is pressed, the elbow formed by assembling and welding is then welded into steel billets and then pressed by the steel plate, and then the three links are pressed.
Pipe fittings are usually welded by manual arc welding, gas shielded arc welding and automatic welding.
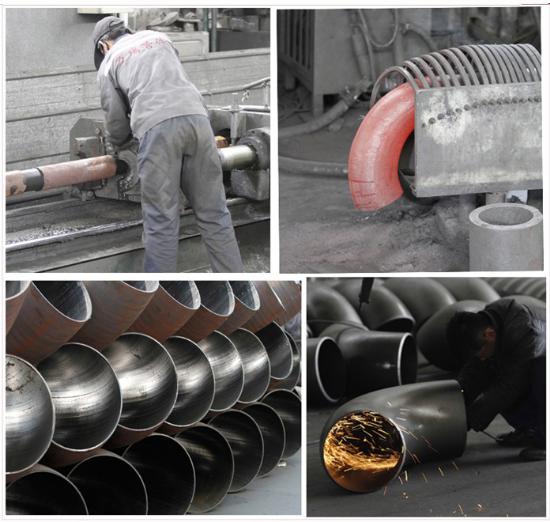
1 inch steel pipe fittings is the most common size.
The manufacturing plant should prepare welding procedures to guide the welding work and evaluate the welding process according to the requirements of the corresponding specifications to verify the correctness of the welding procedures and evaluate the welding ability of the welders. Welders engaged in pipe welding operations shall be able to engage in the welding of relevant steel through the examination of the quality and technical supervision department and the corresponding qualification certificates. (according to the regulations of some industries, the welding pipes in some industries should be used to obtain the welder examination and welding technical evaluation, such as the welding of vessel fittings. " The welder examination and welding procedure qualification of the corresponding classification society must be obtained.
Heat treatment
Heat treatment process is an important part of pipe manufacturing. Through the heat treatment steps of heating, heat preservation and cooling, the processing hardening, residual stress and metal deformation defects produced in the forming process are eliminated, and the metal structure and properties of the tubes after forming are changed, the state before the deformation processing is restored or the performance is improved and raised.
The commonly used heat treatment equipment is a reverberatory furnace, electric furnace, and so on. The usual control mode is that the thermocouple in the furnace is connected to the control device of a temperature time automatic recorder through a sensor. The heat treatment of 1 inch steel pipe fittings is much easier than other bigger size.
There are different regulations for heat treatment in different product standards. Not all deformed tubes are heat-treated. Usually, when the final forming temperature is not less than 723 degrees C (recrystallization temperature) for a tube of low carbon steel, the heat treatment can not be done, because the final state of the tissue is basically a normalizing state under this temperature, below this temperature or higher than 980. Heat treatment should be carried out; the alloy steel or stainless steel fittings should be heat-treated, whether in cold forming or hot forming.
The conventional inspection of heat treatment is usually done by hardness test.
Surface treatment
The surface treatment of pipe fittings is usually made of sand blasting, shot blasting, grinding and pickling to remove the rust and scratches on the surface of the product, so as to make the product smooth and meet the requirements of subsequent processing and inspection.
The surface hardness of tube parts treated with shot blasting is slightly increased.
Cutting machining
Cutting process is the process to finish the welding end, structural dimension and geometric tolerance of pipe fittings. For some pipe products, machining includes internal and external diameter machining. The cutting process is accomplished mainly by special machine tools or general machine tools. For too large size pipes, other methods can be used when the existing machine tools can not meet the processing requirements. For example, the method of grinding after gas cutting is used for large caliber elbow.
The appearance and size inspection of pipe fittings is usually done after cutting.
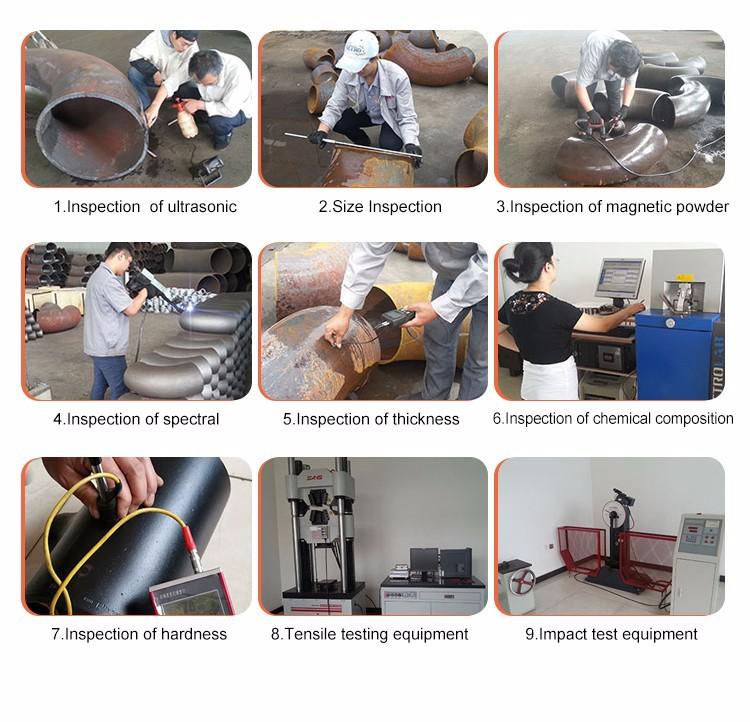
Nondestructive testing
Nondestructive testing is an important procedure for testing defects that may occur in the process of material and pipe fittings. The requirements of NDT for most pipe fittings standards are specified, but the requirements are not consistent. In addition to non-destructive testing of product standards and order requirements, some manufacturers with more stringent quality control also make nondestructive testing requirements according to the material, processing technology and internal quality control regulations to ensure the quality of the factory products. 1 inch steel pipe fittings is the most common products. In actual work, the determination of qualified grade of pipe nondestructive testing should be specified according to the order requirements or standards. Because the surface of the pipe is basically the state of the original tube, plate or forgings, for nondestructive testing of the surface quality of the pipe (MT, PT), the requirement of no definite grade can be classified as grade II. However, no matter how the qualified grade is specified, it is not easy to determine the depth of the interlayer and the crack.