The reasons for the leakage of flange fittings are as follows:
1. Improper installation: If the flange fittings are installed improperly, such as flange bolts not tightened properly or gaskets not placed properly, it may cause leakage. During installation, it must be ensured that the flange bolts are tightened evenly and that proper sealing gaskets are used.
2. Improper selection of materials: Selection of materials that are not suitable for a specific working environment and media may also lead to leakage. Different media have different requirements on the corrosion resistance and pressure resistance of the material. If the selected material cannot withstand the pressure of the medium or cannot resist corrosion, leakage may occur.
3. Uneven flange surface: Uneven or damaged flange surface may also cause leakage. If the flange surface is uneven, the gasket will not fit tightly, resulting in leakage.
4. Aging or wear of the gasket: As the sealing part of the flange pipe fittings, the gasket cannot effectively prevent leakage if it is aged, worn or damaged. Regular inspection and replacement of gaskets is key to preventing leaks.
5. Temperature and pressure changes: Flange fittings work under different temperature and pressure conditions. If the temperature and pressure change too much, it may cause expansion or contraction of flange fittings, thereby destroying the sealing performance and causing leakage.
6. Pipeline vibration or shock: Pipeline vibration or shock may also cause flange fittings to loosen or be damaged, resulting in leakage. In this case, you can consider taking vibration reduction measures or adding pipe supports to reduce vibration and impact.
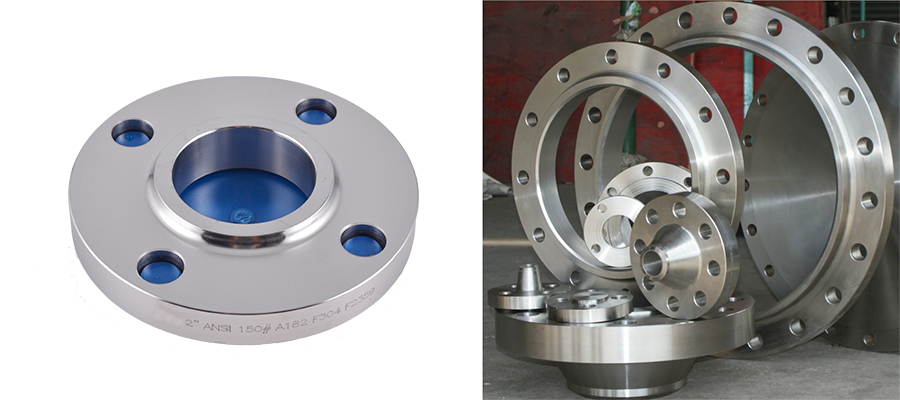
2. Improper selection of materials: Selection of materials that are not suitable for a specific working environment and media may also lead to leakage. Different media have different requirements on the corrosion resistance and pressure resistance of the material. If the selected material cannot withstand the pressure of the medium or cannot resist corrosion, leakage may occur.
3. Uneven flange surface: Uneven or damaged flange surface may also cause leakage. If the flange surface is uneven, the gasket will not fit tightly, resulting in leakage.
4. Aging or wear of the gasket: As the sealing part of the flange pipe fittings, the gasket cannot effectively prevent leakage if it is aged, worn or damaged. Regular inspection and replacement of gaskets is key to preventing leaks.
5. Temperature and pressure changes: Flange fittings work under different temperature and pressure conditions. If the temperature and pressure change too much, it may cause expansion or contraction of flange fittings, thereby destroying the sealing performance and causing leakage.
6. Pipeline vibration or shock: Pipeline vibration or shock may also cause flange fittings to loosen or be damaged, resulting in leakage. In this case, you can consider taking vibration reduction measures or adding pipe supports to reduce vibration and impact.
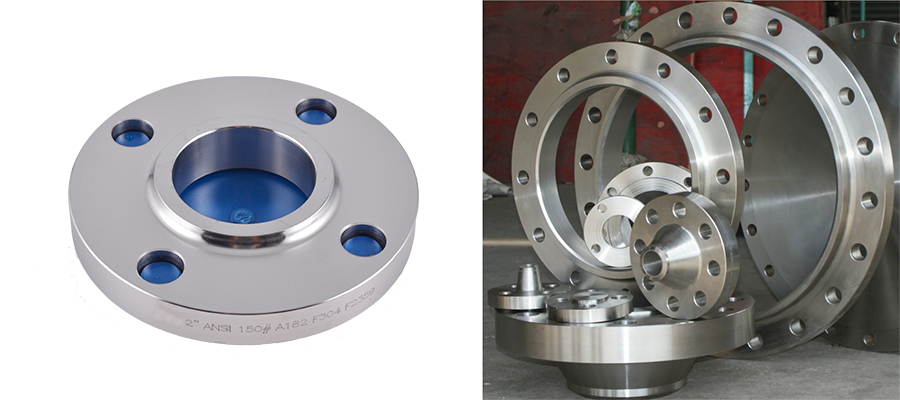
So how to choose a suitable steel pipe flange in the pipeline?
1. Select the material according to the pipe material and medium: select the appropriate flange material according to the material of the pipe and the nature of the medium. Common flange materials include carbon steel, stainless steel, alloy steel, etc. Make sure that the flange material can withstand the temperature, pressure and corrosion of the medium.
2. Select the flange size according to the pipe size: the size of the flange fittings must match the pipe size. The diameter of the pipe determines the size of the flange, for example, choose a flange with the corresponding diameter, such as DN50, DN100, etc.
3. Select the flange level according to the working pressure: select the appropriate flange level according to the working pressure of the piping system. The grade of the flange is classified according to the pressure grade it bears, for example, 150#, 300#, 600# grades in ANSI/ASME B16.5.
4. Consider the working temperature: choose the appropriate flange according to the working temperature of the piping system. High temperature environments may require materials with better high temperature tolerance or special thermal expansion compensation measures.
5. Consider the installation requirements and environmental conditions: select the appropriate flange type according to the installation requirements and environmental conditions. Common flange types include welding flanges, bolted flanges, and clamp flanges. Different types of flanges are suitable for different installation methods and environmental conditions.
6. Follow the applicable standards and specifications: choose the appropriate flange according to the applicable standards and specifications in the area. For example, American standards include ANSI/ASME B16.5 and API 6A, and European standards include EN 1092-1 and DIN, etc.
7. Consider maintenance and overhaul requirements: When selecting flanges, consider the convenience of maintenance and overhaul. Certain flange designs can be easily removed and installed for maintenance and service work.
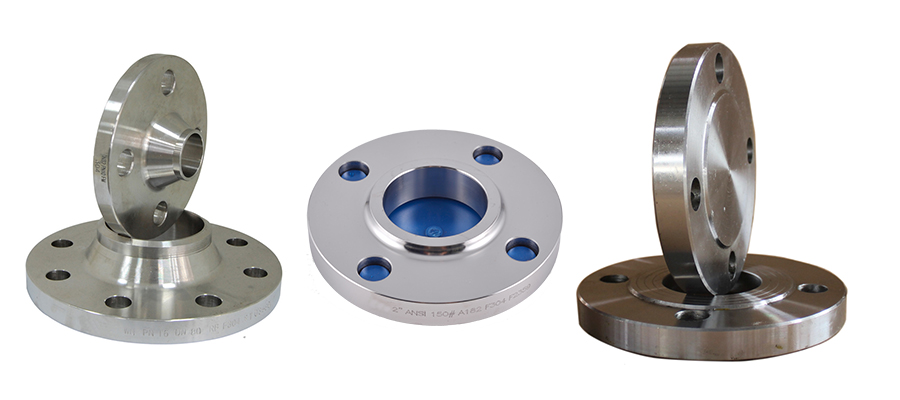
It is important to note that selecting the proper flange requires a combination of factors and should be evaluated against specific piping system and application needs.
2. Select the flange size according to the pipe size: the size of the flange fittings must match the pipe size. The diameter of the pipe determines the size of the flange, for example, choose a flange with the corresponding diameter, such as DN50, DN100, etc.
3. Select the flange level according to the working pressure: select the appropriate flange level according to the working pressure of the piping system. The grade of the flange is classified according to the pressure grade it bears, for example, 150#, 300#, 600# grades in ANSI/ASME B16.5.
4. Consider the working temperature: choose the appropriate flange according to the working temperature of the piping system. High temperature environments may require materials with better high temperature tolerance or special thermal expansion compensation measures.
5. Consider the installation requirements and environmental conditions: select the appropriate flange type according to the installation requirements and environmental conditions. Common flange types include welding flanges, bolted flanges, and clamp flanges. Different types of flanges are suitable for different installation methods and environmental conditions.
6. Follow the applicable standards and specifications: choose the appropriate flange according to the applicable standards and specifications in the area. For example, American standards include ANSI/ASME B16.5 and API 6A, and European standards include EN 1092-1 and DIN, etc.
7. Consider maintenance and overhaul requirements: When selecting flanges, consider the convenience of maintenance and overhaul. Certain flange designs can be easily removed and installed for maintenance and service work.
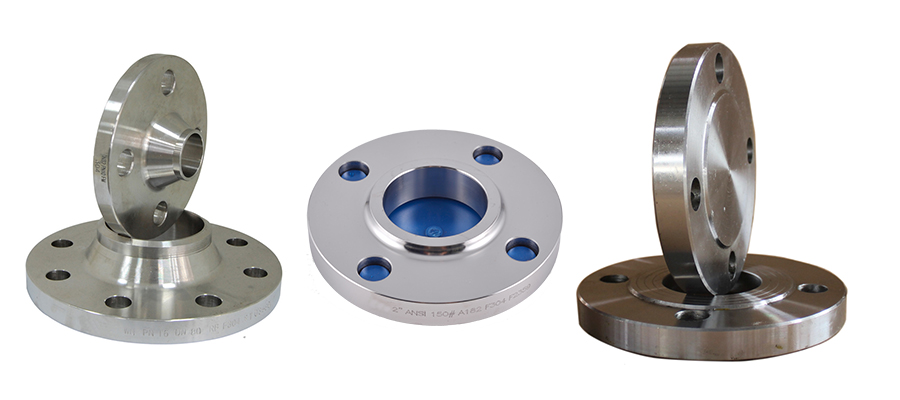
It is important to note that selecting the proper flange requires a combination of factors and should be evaluated against specific piping system and application needs.
Previous:What is the AWWA Class B flange
Next:china manufacturer forging stainless steel socket weld flange
Next:china manufacturer forging stainless steel socket weld flange