Four types of common flange production processes
What are the four common types of flange production processes? There are four main types of flange production processes: forging, casting, cutting and rolling. Compared with forging, forged flanges have accurate dimensions, small processing engineering, and low cost, but they have casting defects such as pores, cracks, and inclusions; forged flanges are relatively Casting flanges have low carbon content, good corrosion resistance, good streamline shape, dense organization and good performance.
(1) Cast flange and forged flange
The cast flange has accurate shape and size of the blank, small processing volume and low cost, but has casting defects (porosity, crack, inclusion); the internal organization of the casting is less streamlined (if it is a cutting part, the streamlined shape is even worse);
Forged flanges generally have lower carbon content than cast flanges and are not easy to rust. Forgings have better streamlined structure, denser structure, and better mechanical properties than cast flanges. Improper forging process will also cause large or uneven grains, hardening cracks, and forging costs. higher than cast flanges. Forgings can withstand higher shear and tensile forces than castings. The advantage of casting is that it can produce a more complex shape and the cost is relatively low;
The advantage of forgings is that the internal structure is uniform, and there are no harmful defects such as pores and inclusions in the casting; the forging process generally consists of the following processes, that is, selecting billets, heating, forming, and cooling after forging. Forging process methods include free forging, die forging and fetal membrane forging. During production, different forging methods are selected according to the quality of the forgings and the number of production batches.
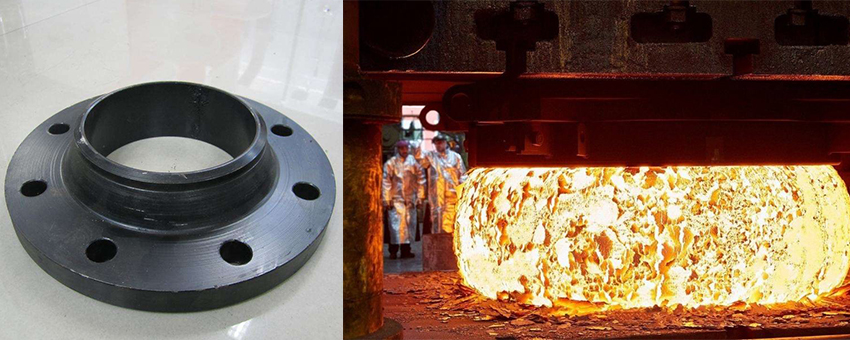
Free forging has low productivity and large machining allowance, but it has simple tools and great versatility, so it is widely used for forging single-piece and small-batch forgings with simple shapes. Free forging equipment includes air hammer, steam-air hammer and hydraulic press, etc., which are respectively suitable for the production of small, medium and large forgings. Die forging has high productivity, simple operation, and easy mechanization and automation. Die forgings have high dimensional accuracy, small machining allowance, and more reasonable distribution of fiber structure, which can further improve the service life of parts.
The basic process of free forging: During free forging, the shape of the forging is gradually forged from the blank through some basic deformation processes. The basic processes of free forging include upsetting, drawing, punching, bending and cutting.
1. Upsetting Upsetting is an operation process in which the raw material is forged in the axial direction to reduce its height and increase its cross-section. This process is commonly used for forging gear blanks and other disc-shaped forgings. Upsetting is divided into two types: full upsetting and partial forging.
2. Elongation Elongation is a forging process that increases the length of the blank and reduces the cross-section. It is usually used to produce blanks for shafts, such as lathe spindles, connecting rods, and the like.
3. Punching is a forging process in which a punch is used to punch through holes or non-through holes in the blank.
4. Bending A forging process in which the billet is bent into a certain angle or shape.
5. Twisting is a forging process in which one part of the blank is rotated by a certain angle relative to another part.
6. The forging process of cutting and dividing the blank or cutting off the head.
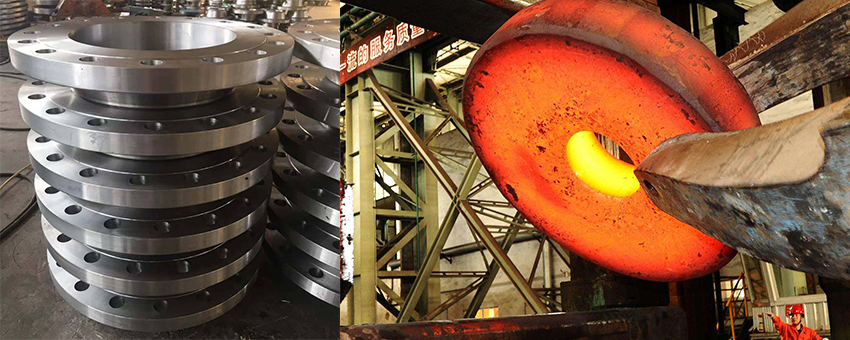
(2) Die forging
The full name of die forging is model forging, which is formed by placing the heated billet in a forging die fixed on the die forging equipment.
1. The basic process of die forging Die forging process: blanking, heating, pre-forging, final forging, punching and skinning, trimming, quenching and tempering, shot peening. Common processes include upsetting, drawing, bending, punching, and forming.
2. Commonly used die forging equipment Commonly used die forging equipment includes die forging hammer, hot die forging press, flat forging machine and friction press.
In layman's terms, the quality of forged flanges is better, generally produced by die forging, with fine crystal structure and high strength, of course, the price is also more expensive.
Whether it is a cast flange or a forged flange, it is a common manufacturing method for flanges. It depends on the strength requirements of the components to be used. If the requirements are not high, turning flanges can also be used.
(3) Cut the flange
The inner and outer diameters and thicknesses of the flange are directly cut on the middle plate, and then the bolt holes and water lines are processed. The flanges produced in this way are called cut flanges, and the large diameter of such flanges is limited by the width of the middle plate.
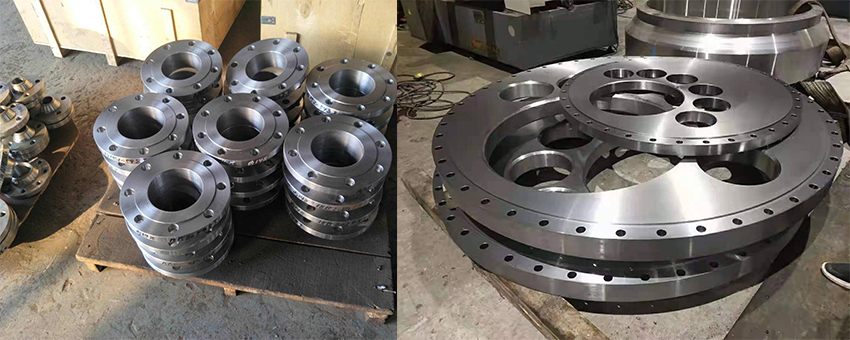
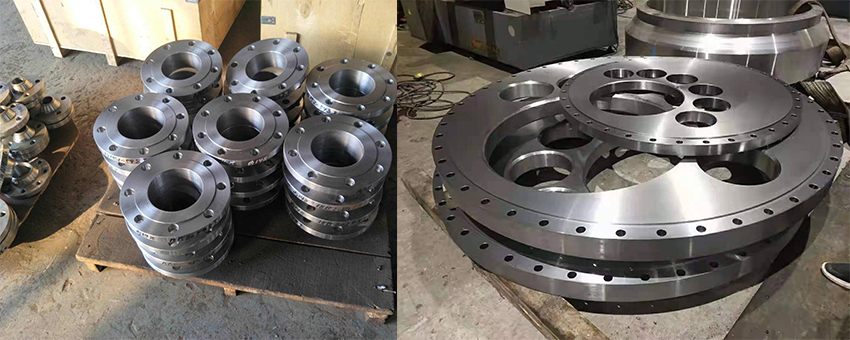
(4) Rolled flange
The process of cutting the sliver with a medium plate and then rolling it into a circle is called rolling, which is mostly used in the production of some large flanges. After the roll is successful, it is welded, then flattened, and then processed in the process of water line and bolt hole.
Four common types of flange production can be selected: forging, casting, rolling and cutting. Among them, cutting flanges are mainly cut and manufactured directly in the middle class, and then bolt holes and waterline processing are performed, while rolled flanges are mainly It is a flange processing process that uses a medium plate to cut a sliver and then rolls it into a circular shape. It is often used in the production, processing and manufacturing of some large flanges, which have advantages and disadvantages.
Previous:What is the protective flaw detection tape of butt welding elbow
Next:How to made four-way pipe fittings
Next:How to made four-way pipe fittings